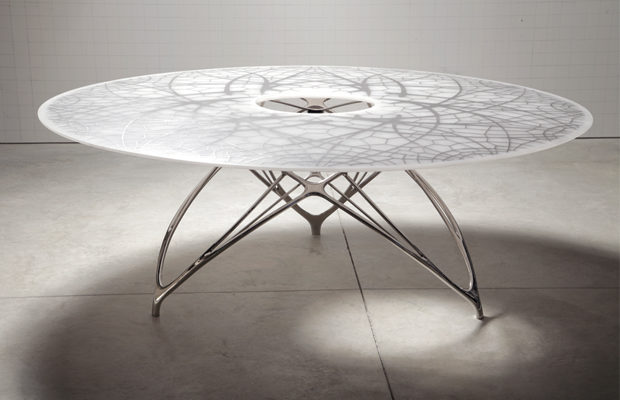
Design
Why Joris Laarman Matters
THREE TIMES IN MY TWENTY-FIVE years of collecting, I have been stopped in my tracks on first encountering the work of a designer: Ettore Sottsass, Gaetano Pesce, and, about eight years ago, the young Joris Laarman. I have followed his career since 2006, when I saw his first works at Design Miami, and he continues to amaze me with each new series.
Laarman is a 2003 graduate of the Design Academy Eindhoven. He gained international recognition with his senior project: a functioning baroque looking radiator named Heatwave. Then, at Design Miami in 2006, he introduced the prototypes of the aluminum armless Bone chair and the resin polyurethane translucent Bone chaise longue (they’re now in the Rijksmuseum and Victoria and Albert Museum, respectively). Both were created using a computer algorithm that mimics the growth of bones. As a radiologist and design lover, I was blown away. I was looking at a modern reincarnation of Carlo Mollino. I spent the next three days analyzing which of these two masterpieces I should buy. There was no right answer. Both were spectacular. I finally picked one—number one of the production of ten chaise longues—only to be sorry later that I didn’t buy both.
I saw Laarman’s work again at Friedman Benda in March 2010. By this time he had extended the Bone series to include an armchair and a rocker. At this exhibition he also introduced the Bridge and Leaf tables, the Starlings coffee table, the Halflife lamp, the bronze Branch bookshelf, the Cumulus coffee table, and the eighteen-foot-tall In Case of a Thousand Books bookcase.

Laarman’s 2014 Maker chairs and tables are created with 3-D-printing, allowing for endless design possibilities in a variety of mediums.
Just recently, in May 2014, at Friedman Benda, I saw a new direction in Laarman’s work. Using 3-D printing, he and his team have developed the Maker series of chairs and tables, which has endless design possibilities. These can be made in different shapes and materials—resin, wood, plastic, and metal—depending on the designer’s will or the client’s wishes. He also showed two Vortex steel bookcases and consoles and two Micro Structure metal chairs that are as aesthetically strong as anything he’s produced previously. The metal-lattice serpentine Dragon bench, shown as a prototype, was extraordinary. It was purchased by the High Museum in Atlanta.
I had been lucky enough to visit Laarman about six weeks earlier in Amsterdam where I saw his MX3D Metal robotic machine extruding the raw metal cables for the production of the Dragon bench. I thought the machine was making Giacometti sculptures right in front of me. When I asked Joris how he was going to take these three-foot pieces of raw metal and produce a twelve-by-eight-foot bench, he just winked and said, “I do not think my team or I are going to get much sleep in the next month.”

Also employing 3-D printing, this prototype aluminum Vortex console starts with an ordinary horizontal shelf at the bottom, with higher shelves becoming more curved and convoluted.
I think what makes Laarman special is his rare combination of math, science, and technology with a very refined design mind. He is tougher on himself than most of his clients are. As a designer using computers, lasers, and 3-D printing, he creates work that stands out for its unique DNA and its beauty. I cannot wait to see what is next.
Photos courtesy of Joris Laarman and Friedman Benda, New York.